Printable aluminum alloy designed to balance strength and cost
Monica Cooney
Apr 30, 2025

Aluminum alloys are widely used in transportation applications because of their high strength-to-weight ratio, as well as their affordability. However, challenges arise when using them in extreme high strength and high temperature applications, particularly in components such as pistons of combustion engines, fan blades of jet engines, and vacuum pumps. At elevated temperatures, few aluminum alloys can block dislocation movements effectively, which controls the strength. Moreover, few of the designs have considered costs and sustainability metrics in the design, which is essential for high-demand industries. Titanium alloys, such as Ti-64, that are often used in fan blades, are not only heavier and not machinable, but also nearly twice as expensive.
Additive manufacturing (AM) is rapidly evolving and providing new pathways for designing innovative alloys. A recent study from Carnegie Mellon University and Massachusetts Institute of Technology (MIT) utilized computational simulations and optimization techniques to identify a new aluminum alloy system that balances strength and cost. The study proposes Al-Ni-Er-Zr-Y (aluminum, nickel, erbium, zirconium, and yttrium) as a class of aluminum alloy that the cost/strength trade-off can be tailored to achieve 95% strength of a benchmark printable Al alloy with 15% anticipated net cost savings. Using the same framework, another room-temperature design was generated that matched the strength of benchmark alloys while achieving 80% cost savings.
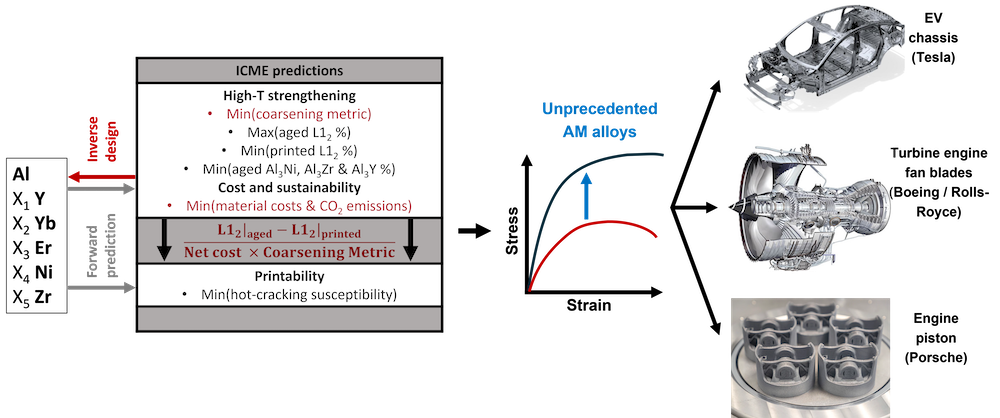
One of the Taheri-Mosavi research group's focus points is "Agile design of new-generation aluminum alloys by exploiting rapid solidification in additive manufacturing"
“The development of these aluminum alloys has the potential to make a significant impact in the automotive industry because of the high demand for high performance alloys with a more sustainable and lower cost materials,” said Assistant Professor Mohadeseh Taheri-Mousavi, who contributed to this research along with current doctoral student Benjamin Glaser.
Using high-throughput calculated phase diagram (CALPHAD)-based integrated computational materials engineering (ICME) simulations together with machine learning techniques, the researchers rapidly explored composition-process–structure–property relationships and identified alloys that could surpass benchmark properties. Laser-based AM offers a higher cooling rate, allowing aluminum alloys to be solidified rapidly and creating new microstructural features. This study exploits metastable phases that precipitates only in rapid solidification to improve the strength.
This research was sponsored by the Army Research Laboratory, United States and was accomplished under Cooperative Agreement Number W911NF-20-2-0175.